組立・メンテナンスを意識したローコスト設計のポイント
油圧配管の見直しで組立工数の削減
機械装置に油圧機器を使用する場合には、油圧配管が必要になります。私も製造部に所属した事があるので配管の曲げ作業はかなり難しく習熟が必要で、施工部位によると思わぬ時間が掛かります。
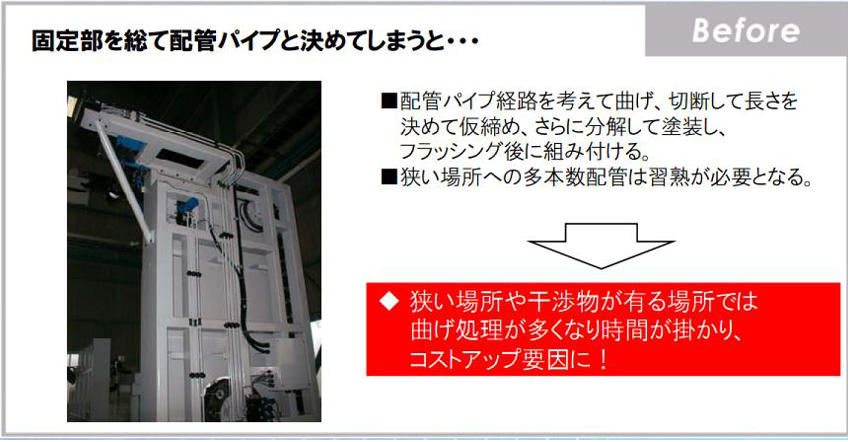
弊社の場合は1台だけのATC装置の設計製作も多々あります。量産機ならば配管曲げ専用の業者様にお願いするのですが、専用機になると現合での配管曲げ作業になります。配管パイプ経路を考えて曲げ、切断して長さを決めて仮締した後、分解して塗装しフラッシング後に組み付ける作業となります。また狭い場所や干渉物がある場合は曲げ処理が多くなりコストアップの要因になります。
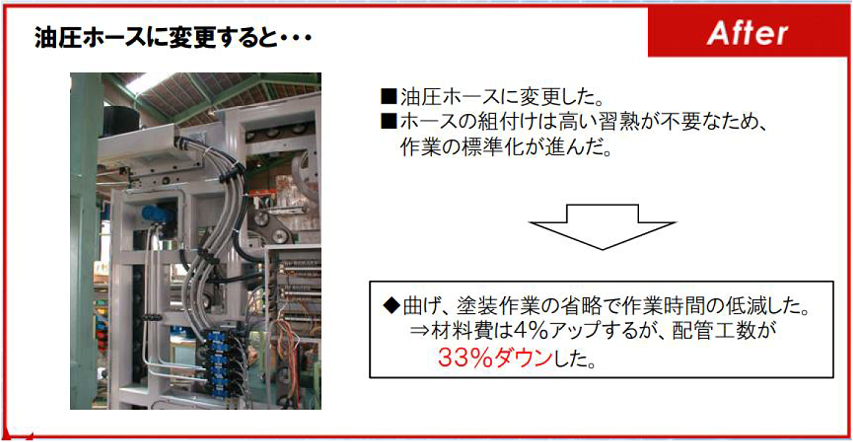
油圧配管を油圧ホースに変更しました。まずホースの組付けは高い習熟が不要なため作業の標準化が進みました。配管パイプとの比較とすると曲げ作業・塗装作業の省略で作業時間の低減ができました。材料コストはUPしますが、配管作業にかかる工数が削減されコストダウンになりました。注意点としましてホース金具のカシメ作業に専用工具、機器が必要となる事と油圧ホース特有の脈動があるので支持方法に注意が必要となります。
駆動部の分割でメンテナンス性向上
弊社のATC装置装置で、以前は油圧駆動部の一体型駆動ユニット(油圧モーター+電磁弁+コントローラー)を使用していました。
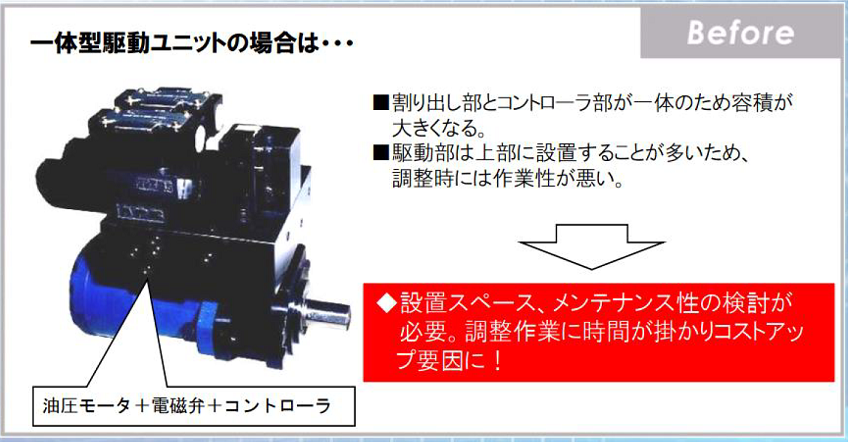
一体型駆動ユニットの場合、割出し部とコントローラー部が一体のため容積が大きくなります。ATC装置では駆動部が上部に設置されてるケースが多いためメンテナスや調整時作業に時間がかかりコストアップの要因になっていました。
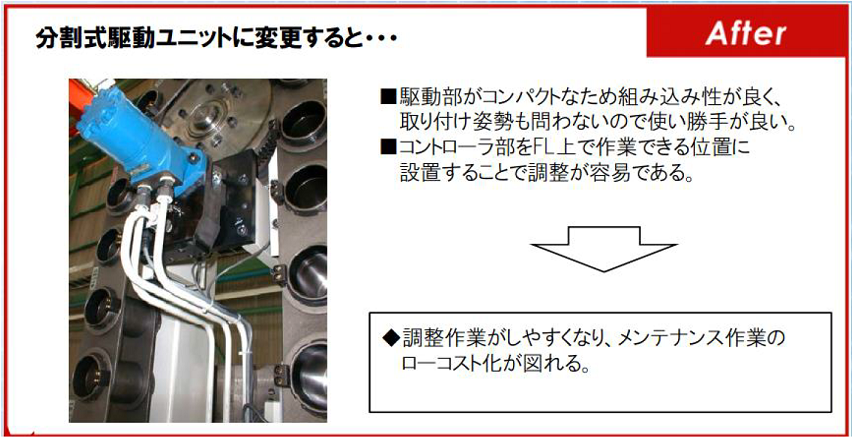
油圧モーターと電磁弁・コントローラーを分割し分割式駆動ユニットに変更しました。このことにより駆動部がコンパクトなため組み込み性が良く取付け姿勢も問わないので使い勝手が良くなりました。またコントローラー部をFL(フロアーレベル)で作業できる位置に設置することで調整が容易になりました。よって調整作業がしやすくなり、メンテナス作業のローコスト化が図れるようになりました。現在も弊社のATC装置に採用しており全国各地や海外でも活躍中です。
機械組立と電装作業を平行作業化
機械組立作業と電装作業が別日程の場合
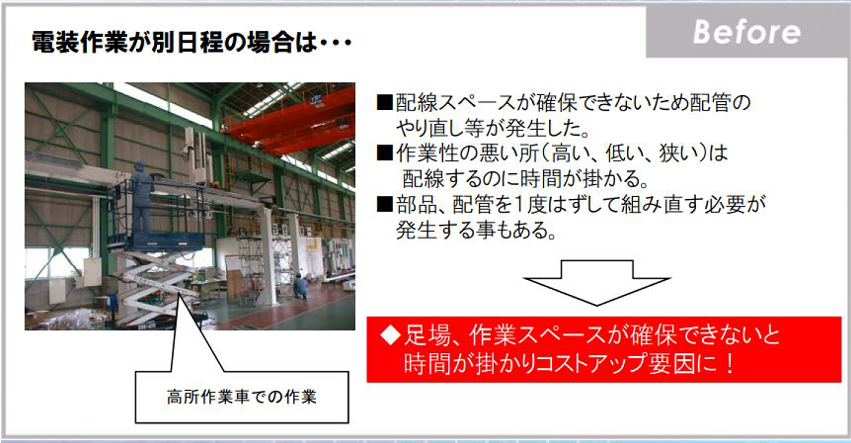
電装作業が別日程の場合は、組立完了のため配線スペースが確保できないため配管のやり直しが発生したり、作業性の悪いところ(高い、低い、狭い)は配線作業に時間がかかったりします。またせっかく組んだ部品や配管など1度はずして組み直す2度手間等が発生することがあります。足場、作業スペースが確保できないと時間がかかりコストアップの要因になります。
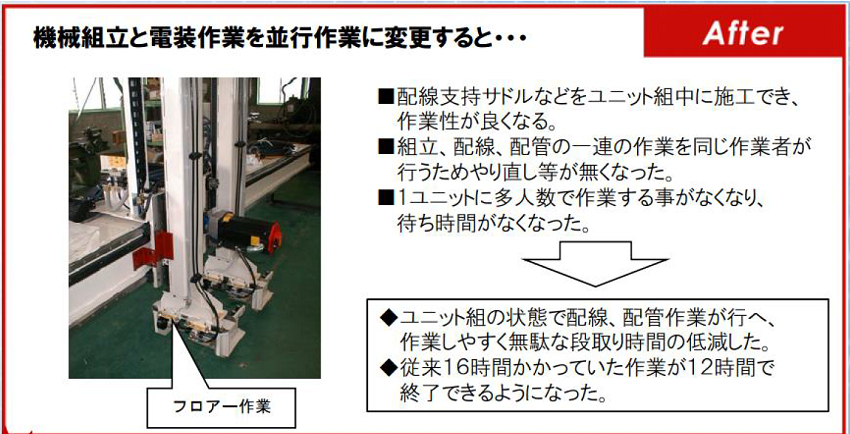
機械組立と電装作業を並行作業に変更すると組立、配線、配管の一連の作業を同じ作業者が行うためやり直し作業等がなくなりユニット組の状態で一連の作業が行えて作業しやすく無駄な待ち時間や段取り時間の低減になりました。この作業を行うには組立作業者の電装知識がある程度必要となります。弊社組立では以前から1人作業制を取り入れています。
エイ・テイ・シイ(株)では今後もローコスト設計のポイントを紹介させて頂きたいと思います。少しでも皆様のお役に立てれば幸いです。今後ともどうぞよろしくお願い申し上げます。